Quality Assurance Excellence Project
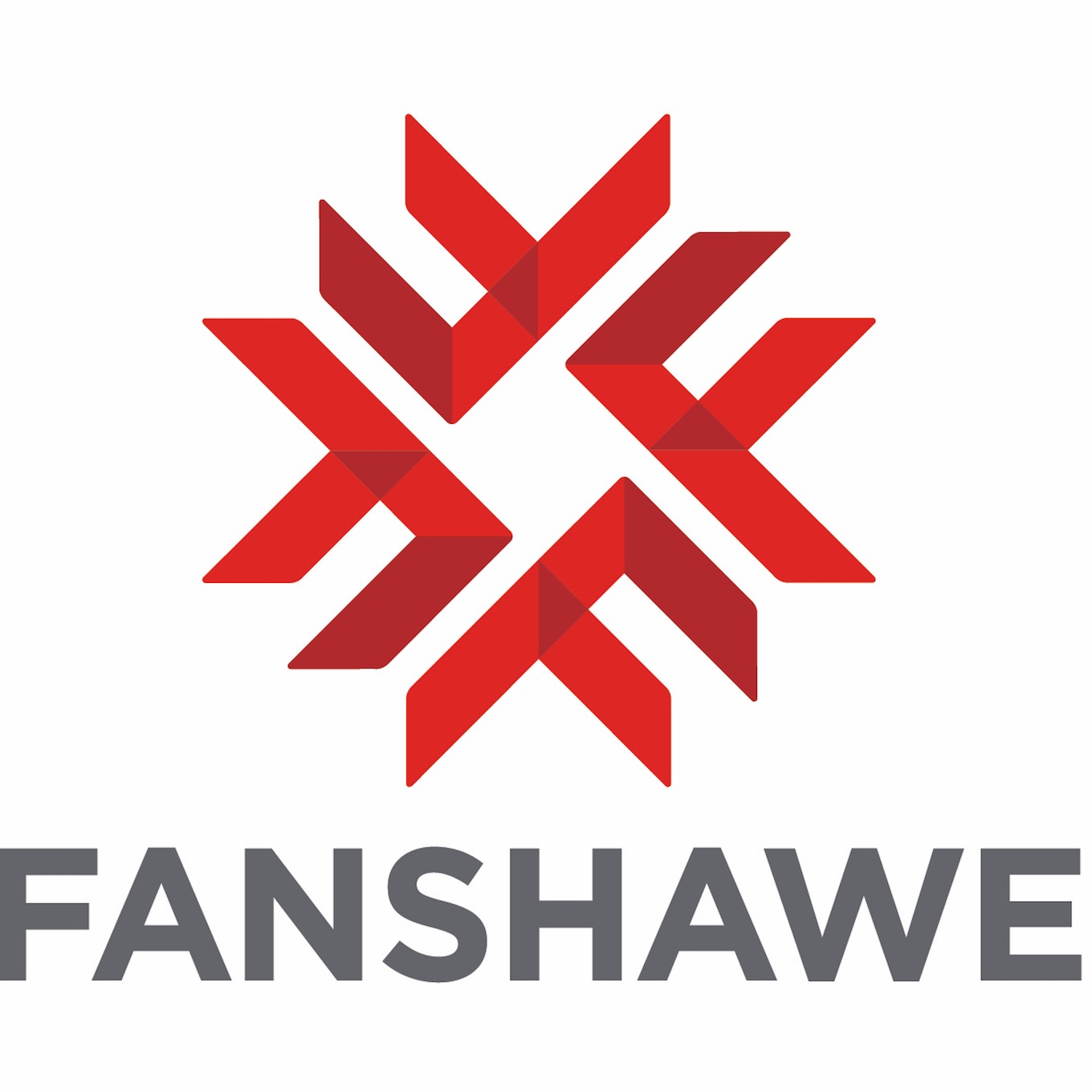
Timeline
-
January 29, 2025Experience start
-
March 18, 2025Mid term Capstone review
-
April 26, 2025Experience end
Timeline
-
January 29, 2025Experience start
-
March 18, 2025Mid term Capstone review
Groups present their capstone project progress addressing challenges and refining project plans
-
April 26, 2025Experience end
Experience scope
Categories
Risk, audit and compliance Information technology Mechanical engineering Healthcare Scientific researchSkills
quality management systems quality control root cause analysis process improvement quality auditing quality assurance quality management management checklistsThis experience is designed for learners in a Quality Assurance Management program, who have developed a comprehensive understanding of quality management principles and tools. Participants are equipped to apply their theoretical knowledge and practical skills to real-world projects, focusing on ensuring quality in various processes and systems. The experience aims to bridge classroom learning with industry applications, enabling learners to effectively implement and manage quality systems across different sectors.
Learners
- Quality audit reports with actionable insights
- Process improvement plans
- Quality control checklists and protocols
- Root cause analysis documentation
- Quality management system implementation guides
Project timeline
-
January 29, 2025Experience start
-
March 18, 2025Mid term Capstone review
-
April 26, 2025Experience end
Timeline
-
January 29, 2025Experience start
-
March 18, 2025Mid term Capstone review
Groups present their capstone project progress addressing challenges and refining project plans
-
April 26, 2025Experience end
Project Examples
Requirements
- Developing a quality control checklist for a manufacturing process
- Conducting a quality audit for a service-based company
- Creating a process improvement plan for a logistics operation
- Implementing a quality management system for a small business
- Performing root cause analysis for recurring defects in a production line
- Designing a training program for quality assurance best practices
- Evaluating supplier quality assurance processes
- Assessing compliance with industry quality standards
Additional company criteria
Companies must answer the following questions to submit a match request to this experience:
Will learners have an opportunity for feedback on their final presentations?
Timeline
-
January 29, 2025Experience start
-
March 18, 2025Mid term Capstone review
-
April 26, 2025Experience end
Timeline
-
January 29, 2025Experience start
-
March 18, 2025Mid term Capstone review
Groups present their capstone project progress addressing challenges and refining project plans
-
April 26, 2025Experience end